Technology options
- RIM – Reactive injection
- RRIM – Reactive injection containing fillers
- SRIM – Structural reactive injection moulding (containing 2D or 3D reinforcements)
The required conditions for this process are the very low viscosity of the injected mass at a lower temperature than the temperature of the mould.
DCPD-RIM
Dicyclopentadiene-based reactive injection technology is suitable for the production of large exterior parts for trucks, buses, construction machinery and agricultural vehicles.
The parts are characterized by their high resistance to stress.
PU-RIM
Reactive casting technology enables the very flexible setting of the properties of polyurethane parts (compact, lightweight, soft, hard, elastic).
PU-RIM is suitable for the production of small and large parts.
PA-RIM
Reactive injection technology enables the very flexible adjustment of the properties of polyamide parts (hard or elastic) with the possibility of direct recycling.
Advantages of RIM technology
- less investment in moulds and injection units;
- easier filling of complicated and large parts;
- optimization of properties with respect to specific requirements.
RIM technology is optimal for series production ranging from hundreds to tens of thousands of parts.
Tailor-made applications
We develop, manufacture and supply parts for major manufacturers throughout Europe.
At Promens Zlín, we choose a combination of technologies according to efficiency, seriality, material and production price according to the required cost / performance ratio.
As a standard, we also address the requirements of Advanced Logistics. Our advantage is that after R&D and production we can supply parts assembled into Just in Time assembly units. We are a partner for manufacturers and for Just in Sequence deliveries.
With these solutions, we help customers be successful in the market.



















We work for the best



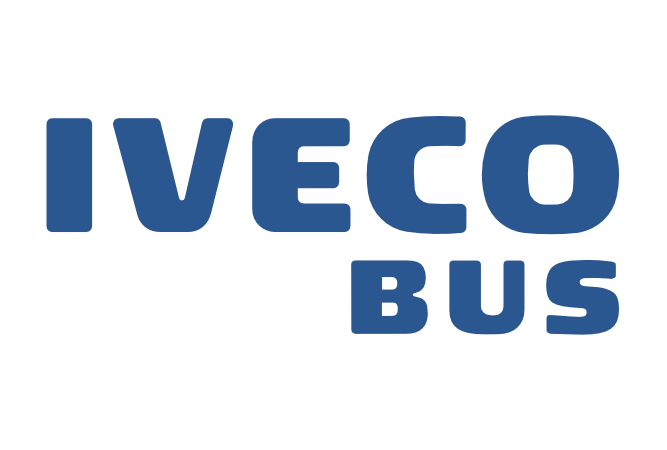

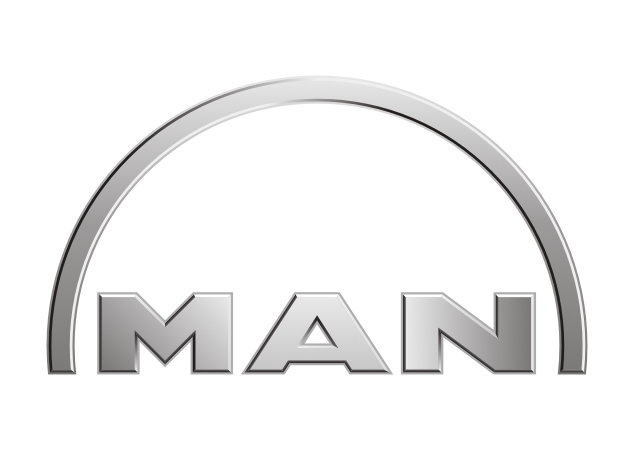


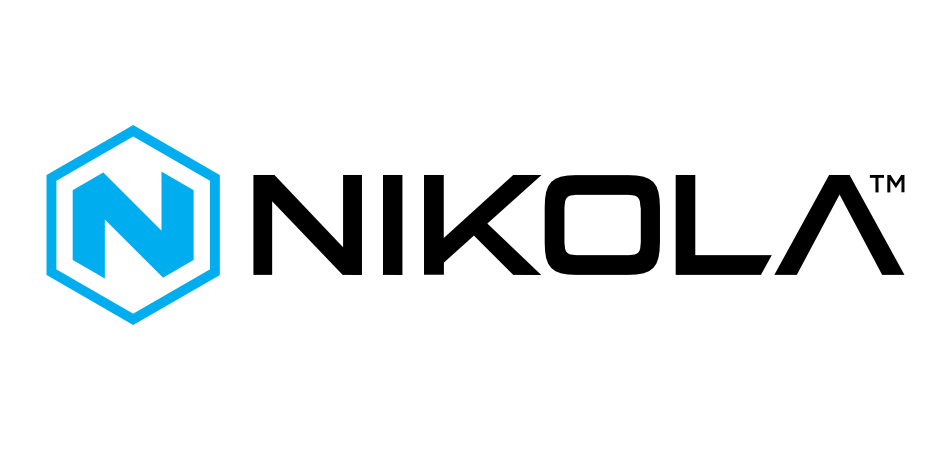


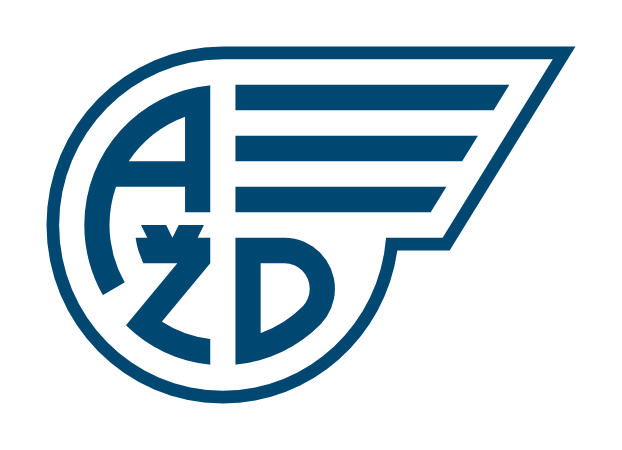
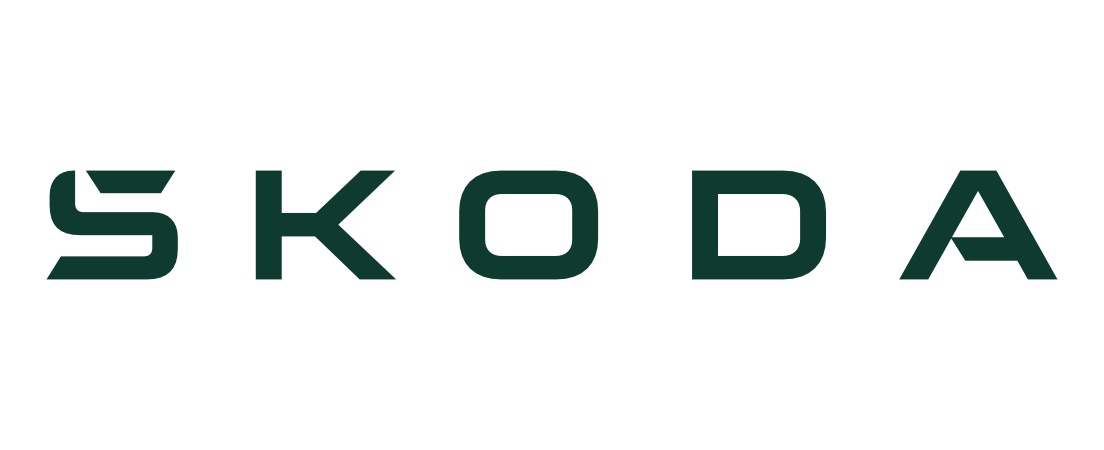
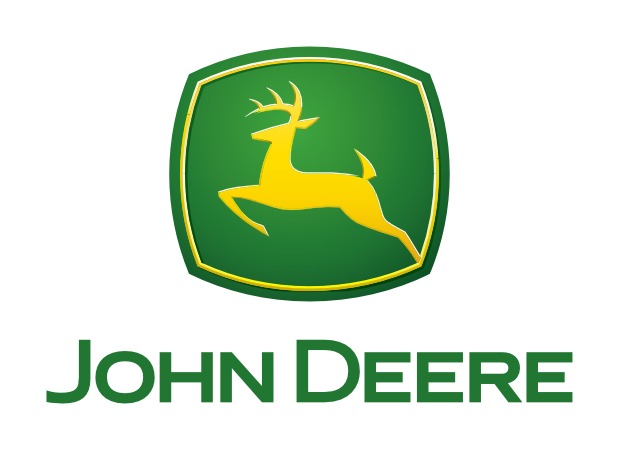



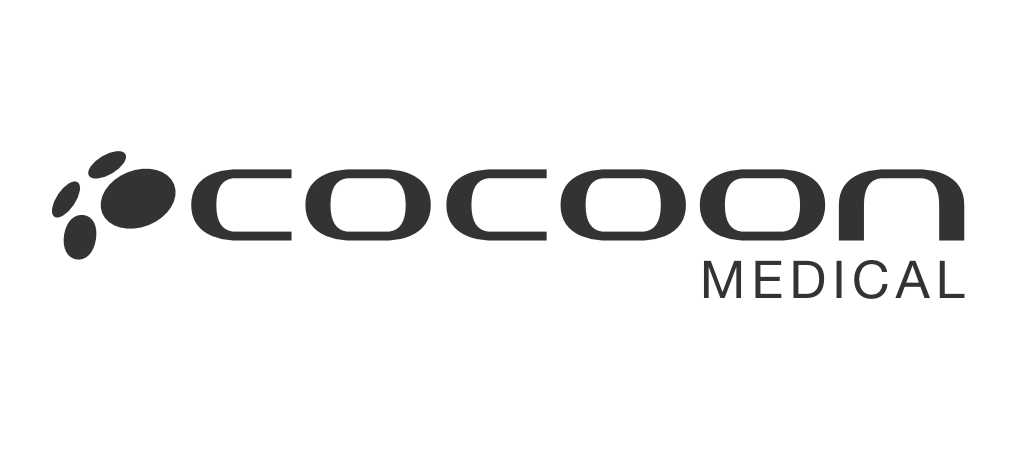


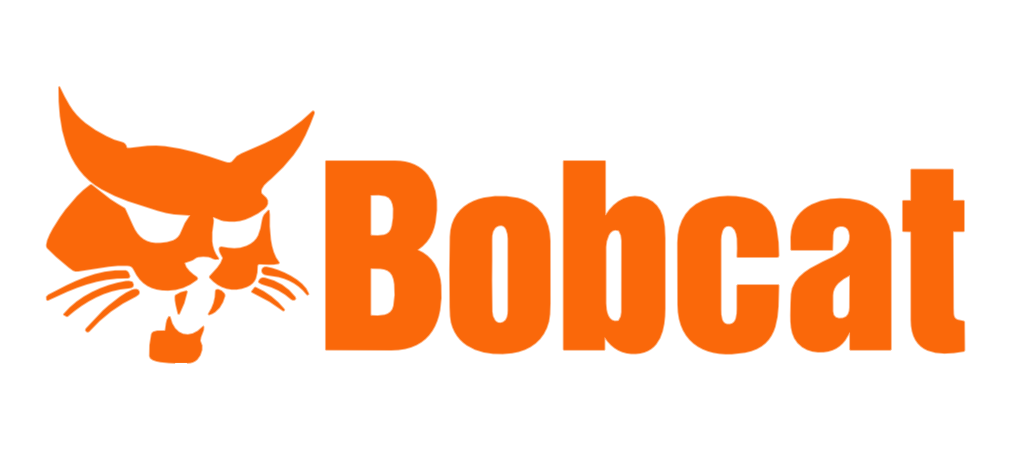
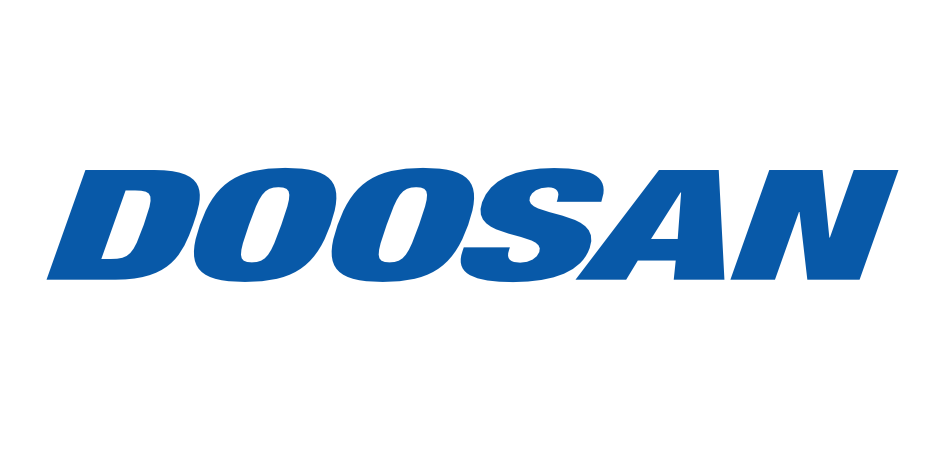




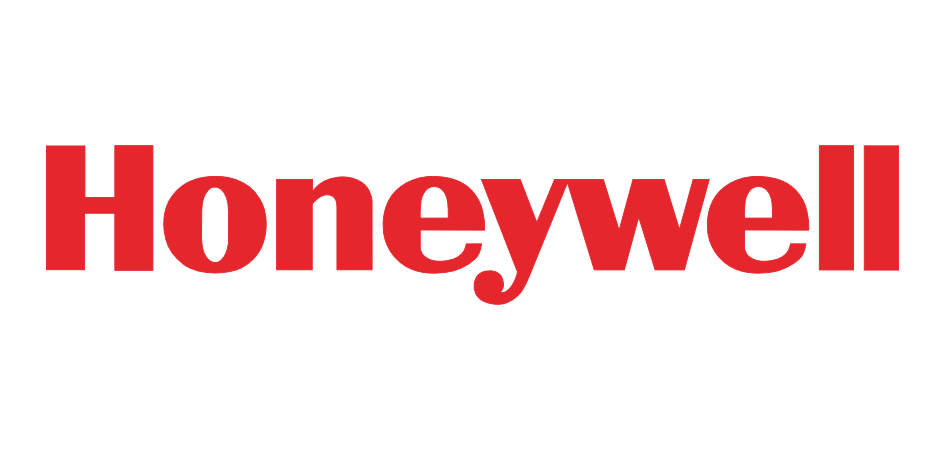
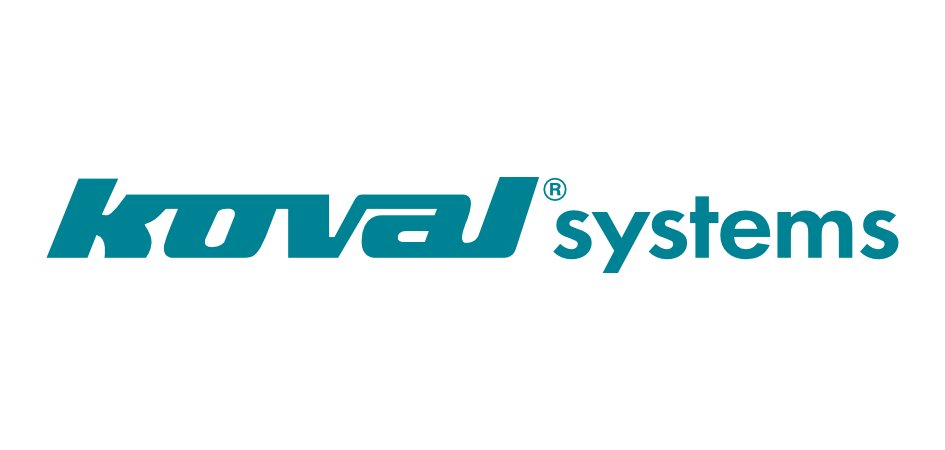
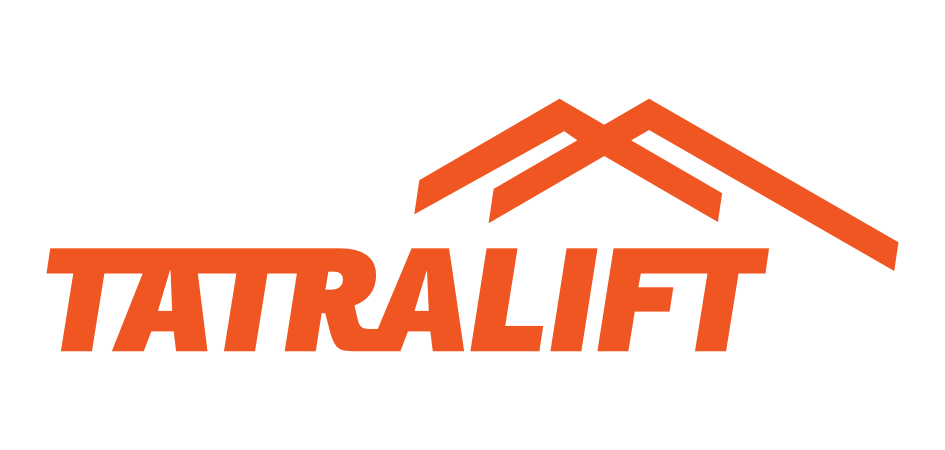
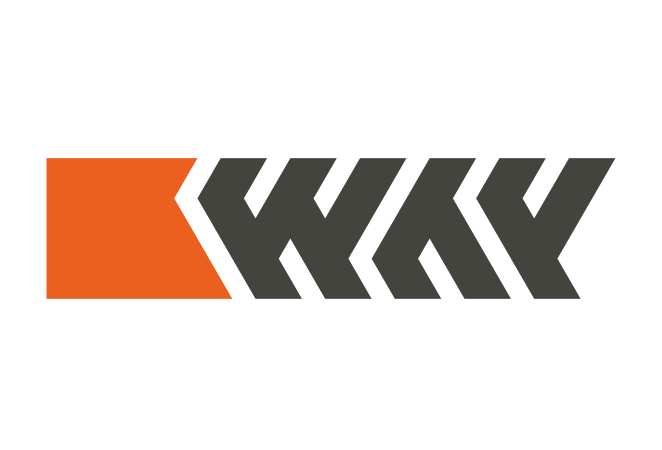
Photos from production
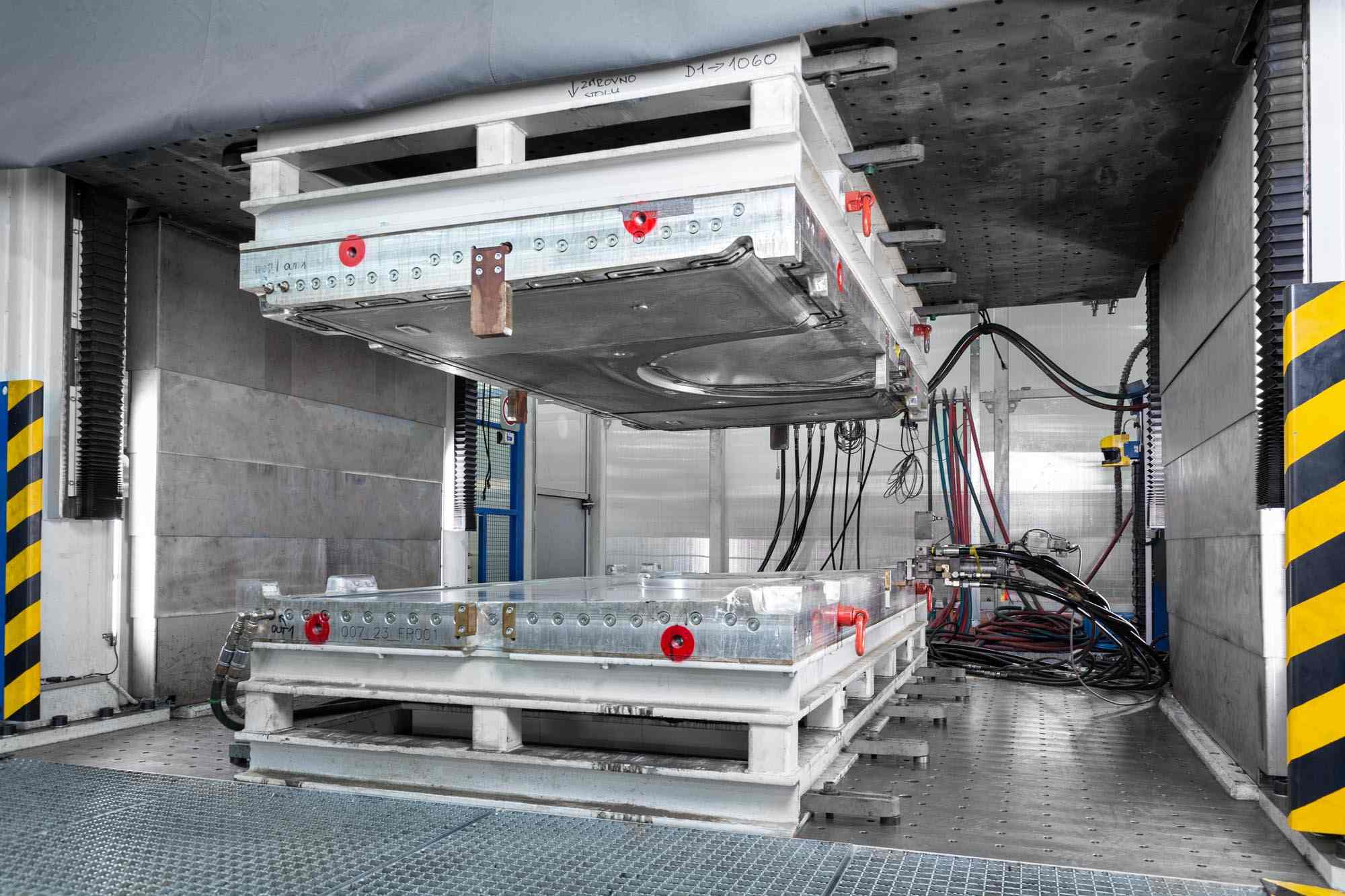


RESEARCH AND DEVELOPMENT | PRODUCTION | PAINTING | ASSEMBLEMENT | JUST IN TIME & JUST IN SEQUENCE
We are experienced Tier 1 development suppliers.
Together, we will make your project succeed.
Call Us
+420 577 051 154
Mail Us
zlin.sales@promenszlin.com
